 |
|
 |
 |
 |
- Baggers
Magazine - May, '08
- American
Iron Retailer - March-April,
'08 - Product Review
- American
Iron Retailer - March-April,
'08 - Showcase
- Drag
Specialties –
Magazine, Nov/Dec ‘07
- AMD
- August, '07 - Out
Braking the Competition
- Speed
- July, '07 - Tech Feature
- American
Bagger - August, '07
- Tech
- Barnett's
- July, '07
- V-Twin
- August, '07
- HOT
ROD's Bike Works, February,
'07
- HOT
BIKE - JULY, '06
- V-TWIN
- JUNE, '06
- THUNDER
PRESS - JUNE, '06
- THUNDER
PRESS - OCT, '05
- EASY
RIDERS MAGAZINE - OCT,
'04
|
|
|
Drag
Specialties - Nov/Dec, '07 >
Spotlight
Spotlight:
Lyndall Racing Brakes
The
Flip Side of Speed
Lyndall Racing Brakes
Gets It Done
800.400.9490
www.lyndallracingbrakes.com
|
|
There’s
a lot of talk in the Harley
world about horsepower
– how much you want,
how to get it, and how
much you’re willing
to pay for it. But all
the noise about going
fast seems to ignore the
fact that you have to
stop sometimes, and the
faster you go, the quicker
you’re going to
need to stop. And horsepower
isn’t the only reason
Harleys can benefit from
better braking –
just ride a heavily loaded
touring bike and you’ll
understand that weight
puts a strain on brakes,
too. So what’s the
easiest way to improve
braking, and also eliminate
dust and squeal at the
same time? Brake pads
from Lyndall Racing Brakes.
Paul Kittrell began his
education in friction
materials when he worked
for the largest West Coast
supplier of friction materials
for race car applications.
“It started out
as a warehouse position
where I was ‘schlepping’
brakes around and helping
the production department
with special orders and
cross-drilling rotors,”
Kittrell says. “Then
I graduated to working
with them on the race
cars.” |
|
Working
on race car brakes was
an education for Kittrell,
who was at the time a
club-level motorcycle
road-racer. He learned
the ins and outs of friction
materials, and why some
work and some don’t.
But the whole time he
was working on four-wheelers,
his heart was in two-wheelers.
He took every nugget of
information he learned
about how each one could
be applied to bikes.
|
|
Eventually,
his head full of
knowledge, he quit
his job and struck
out on his own.
But is wasn’t
as easy as it sounds
to apply car technology
to motorcycles.
Cars use cast-iron
brake rotors, for
example, while motorcycles
use stainless-steel
rotors. A pad compound
that works well
with one might not
work at all with
the other. So he
entered a re-learning
phase, and by the
time he was finished
he was ready to
realize the American
dream and start
his own brake-pad
company.
Initially
Kittrell made brakes
for road-racing
and high-performance
sportbikes. |
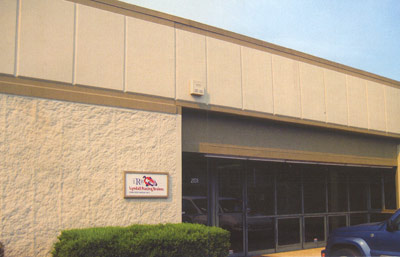
Lyndall
Racing Brakes
is a family-owned
and operated
American
manufacturer
of premium
quality
V-Twin brake
components.
|
|
|
It
was his father who pointed
out that the Harley market
was growing, and so Lyndall
Racing brakes turned its
attention to bringing the
same superior braking to
Harleys as it had to sportbikes. |
“When we first got
into the Harley market,
the biggest thing was
brake squeal,” Kittrell
recalls, “but a
lot of the independent
shops were looking for
an improvement in braking.
One by one we switched
them over to Lyndall because
our pads had superior
service life and better
stopping power, and because
they didn’t generate
dust or scratch up the
rotors.”
Lyndall
Racing Brakes’ pads
are made of a carbon/Kevlar
compound. There are two
basic types of brake-pad
compounds, according to
Kittrell, sintered metal-stock
on Harleys-and organic.
“Most of the organic
pads are made of carbon/Kevlar,
which is good,”
he says. “But saying
your pad is made of carbon/Kevlar
is like saying your tires
are made out of rubber
– it doesn’t
tell the whole story.
What makes the difference
in ours is that we use
the most expensive aramids
you can use in the manufacturing
process.”
How they’re made
sets Lyndall’s pads
apart from the crowd as
much as what they’re
made of. “All our
pads are hand-run,”
Kittrell says. “The
aramids are all measured
in grams and hand-mixed.
We have a couple of guys
running the press, making
sure the temperature and
pressure and the cooling
cycles are all correct.
“
Heat
is what brake pads are
all about, but cooling
is important in the manufacturing
process. “After
the pads cure, we put
them through an extra
heat cycle. The cooling
is typically much slower
on this second operation.
This does two things.
It burns off the residual
phenolics used in the
bonding process, and it
softens the pad slightly,
almost like annealing
it. That’s why the
pads don’t have
to be put through another
major heat cycle to be
broken in. Just put them
in, and within 20-50 miles
you’ll have absolutely
incredible brakes.”
Kittrell says his carbon/Kevlar
pads are superior to the
stock sintered-metal pads
in Harleys both in terms
of performance and service
life. “Our compound
lays down a material transfer
right on the brake rotor,
effectively making the
rotor an 11.5 inch brake
pad turning against two
smaller brake pads. Sintered
metal relies on a chemical
reaction to provide stopping
power, but it changes
the pads so they’re
not the same pads as they
were new.”
|
|
Lyndall’s
pads outlast the stock
pads by a wide margin,
too. “Our pad’s
material transfer is very
protective of the rotor
and runs maybe 30 percent
cooler than a sintered
pad. And it has double
the life expectancy. We
guarantee our Z Plus pads
will go 18,000 miles on
the rear of a 2,000-and-later
bagger – the stock
pads typically last 5,000
– 7,000 miles.”
Whether it’s a hot-rod
solo ride or a two-up
touring rig, good brakes
are important, and Lyndall
Racing Brakes pads for
Harleys are second to
none. Talk to your Drag
Specialties rep about
stocking brake pads from
Lyndall Racing Brakes,
because even though every
bike has to stop sometime,
your parts sales don’t. |
|
|
|
|
|
|
|
 |
 |
|
|
|
|
|