 |
|
 |
 |
 |
- Baggers
Magazine - May, '08
- American
Iron Retailer - March-April,
'08 - Product Review
- American
Iron Retailer - March-April,
'08 - Showcase
- Drag
Specialties –
Magazine, Nov/Dec ‘07
- AMD
- August, '07 - Out
Braking the Competition
- Speed
- July, '07 - Tech Feature
- American
Bagger - August, '07
- Tech
- Barnett's
- July, '07
- V-Twin
- August, '07
- HOT
ROD's Bike Works, February,
'07
- HOT
BIKE - JULY, '06
- V-TWIN
- JUNE, '06
- THUNDER
PRESS - JUNE, '06
- THUNDER
PRESS - OCT, '05
- EASY
RIDERS MAGAZINE - OCT,
'04
|
|
|
American
Iron Retailer - March-April,
'08 >
Product Review
Brake
Pads And Calipers
Lyndall
Racing Brakes And Hawg
Halters Inc.
800.400.9490
www.lyndallracingbrakes.com
Over
The Counter
By: Paul Kittrell
and Mark Thompson |
|
(Download
the article in PDF format
here.)
(Click
here
to read the American Iron
Retailer "Showcase")
|
|
THERE
HAVE BEEN A number
of new developments in braking
systems over the past several
years. We spoke with Paul
Kittrell, founder and president
of Lyndall Racing Brakes,
and Mark Thompson, owner
of Hawg Halters Inc. to
find out which brake pads
and calipers are best suited
for each application, and
how to best sell these braking
solutions. — MK
|
Lyndall
Racing Brakes
Lyndall Racing Brakes has
been in business for 10
years. I started the business
in 1998 with a solidbackground
in premium friction materials
from my sevenyear tenure
at Porterfield Enterprises,
the largest supplier of
friction material for racecar
applications on the West
Coast. As a club-level motorcycle
racer, I was unimpressed
with what was available
in the market for motorcycle
brakes. So, in my spare
time, I began hand-cutting
brake pads, from the same
premium friction materials
used in racecars, for AMA
superbike racers. The racetrack
was the testing ground and
theater of validation for
Lyndall’s products.
One year later, in 1999,
production of brake pads
for Harley-Davidson motorcycles
began. We have since expanded
our products to fit all
American cruiser applications
as well as many others. |
 |
Because
Lyndall has chosen to focus
on the Vtwin market segment,
our production runs are
typically smaller than other
brake-pad manufacturers
who typically merchandise
mass-produced brake pads
for everything with wheels.
This allows greater quality
control and more focused
research and development
of our products. This boutique
business concept also allows
the company to provide superior
customer service, as Lyndall
is committed to 100-percent
customer satisfaction, going
so far as to offer a money-back
guarantee on all our products,
unlike any other brake-pad
manufacturer. |
|
Brakes
Are Not Created
Equal
Lyndall has found
that one of the
best ways to discern
high-quality brake
pads from others
on the market, independently
and without bias,
is by logging onto
some of the motorcycle
forums on the Internet
to get the facts
straight from the
riders themselves.
A forum provides
feedback from a
wide crosssection
of riders from all
around the world.
Everyone loves to
express his opinion,
and the Internet
is one place to
do that freely.
So you’ll
find straightforward
talk about products
— no holds
barred. Short of
your own independent
research, the old
adage stands true:
you get what you
pay for. Premium
components don’t
come cheap, but
they can save much
time and aggravation.
Fix it right the
first time, and
you’ll earn
your customer’s
loyalty, possibly
for life.
Since
not all brake pads
are created equal,
some technical information
can help you understand
the differencesbetween
the kinds available
on the market. There
are three types
of friction material
commonly used for
motorcycle brakes:
sintered metal,
ceramic, and Carbon-Kevlar.
Sintered-metallic
brake pads, which
have a high metal
content, are typically
hard and abrasive
to the rotor surface
while offering moderate
stopping power and
mechanical strength.
Service life tends
to be |
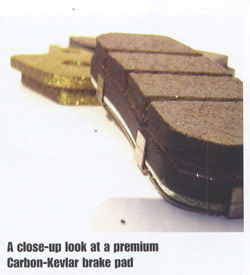 |
significantly lower,
and sintered-metallic
pads tend to run
more dirty and noisy
than other types
of friction material.
They are also inexpensive
to manufacture and
are the cheapest
pads on the market.
Ceramic
brake pads usually
have a high copper
content and are
sintered as well.
While ceramic pads
generally offer
a slightly longer
service life and
run cleaner than
sintered-metallic
pads, they
offer only moderate
stopping power.
Carbon-Kevlar pads,
often referred to
as organic pads,
usually have a small
percentage of iron
or nonferrous metal
and are softer than
other friction materials.
Carbon-Kevlar pads
typically run clean
and quiet, and offer
good stopping
power. They have
an extremely long
service life and
are not abrasive
to the rotor because
they generate less
heat than other
friction materials.
Lyndall’s
brake pads are of
the Carbon-Kevlar
variety. What makes
Lyndall’s
pads unique is that
they contain a premium
blend of Carbon-Kevlar
and nonferrous metal
and have a high
transfer rate. Once
the pad material
has transferred
a layer to the rotor,
the rotor effectively
becomes one big
brake pad, stopping
against the two
smaller brake pads
positioned in the
caliper. The result:
incredible stopping
power, no dust,
no noise, no drag,
no measurable rotor
wear, and the highest
service life of
any pad on the market.
Finding out which
brake pads work
with a particular
caliper can be a
challenge, but most
manufacturers (Lyndall
included) list application
information, complete
with OE part numbers
crossreferenced,
on their web sites.
Also, a phone call
to a rep for those
hard-toidentify
pads can help provide
an answer. By looking
at your sales andservice
history, you can
also identify which
models are the most
popular in your
dealership. Those
would be the best
ones to keep in
stock. Keep in mind
that the older-model
bikes are a diminishing
market segment,
so it’s best
to limit your stock
to one or two of
each fitment.

Safety,
Service, And Sales
As
a safety precaution,
shop owners and
their technicians
should always look
at brake pads whenever
a bike comes into
the shop for any
type of service
or repair work.
While brakes are
a known safety item,
premium-quality
brake pads are also
a great customer
service item that
can enhance the
pleasure of your
customer’s
riding experience.
Installing a brake
pad that solves
the rider’s
dust or noise problems
can boost confidence
in your service
department and increase
repeat business.
The brake pad is
just one component
of an entire braking
system. This system
needs regular check-ups
and maintenance.
Lyndall recommends
cleaning the pistons
located in the caliper
with every brake
pad service. A step-by-step
guide to this process
can be found on
the Service/Tech
page of our web
site. You may also
request a brochure
detailing the process
directly from the
company. Steel-braided
brake lines and
high-performance
brake pads and calipers
are the best upgrades
you can make to
a brake system.
Remember also that
without good tires,
premium brakes cannot
be nearly as effective.
Be sure to check
tire pressure regularly,
but not until the
tires reach optimal
operating temperature;
about 30 minutes
into a ride.
Brake
pads should be displayed
in a manner that
is inviting to the
customer. When shopping
for anything, brakes
included, tactile
sense is important.
People like to touch,
pick up, and examine
when making a choice.
Nine times out of
10, if a customer
picks up the part
he’s considering
and holds it in
his hand, he’ll
buy it. Product
displays should
be accompanied by
informational brochures
and pamphlets for
the customer to
review while waiting
or to take with
him to consider
for a later purchase.
Banners and posters
explaining the products
can also create
excitement and stir
curiosity. Potential
margins for selling
Lyndall’s
pads range from
30 percent to 40
percent. Remember
that the more profitable
you are, the better
customer service
you’ll be
able to provide,
and the happier
your customers will
be.
Hawg
Halters Inc.
Hawg
Halters Inc., also
known as HHI, started
up in 1999 to meet
the customer desire
for improved braking
performance over
the stock H-D product,
and to provide a
custom-styled product
adaptable for a
variety of applications.
HHI has dedicated
itself to supplying
the aftermarket
with a top-quality
brake caliper that
performs well and
has a smooth, clean,
custom appearance,
all at an affordable
price. We also specialize
in braking systems,
so we have the widest
array of products
to fit most any
application. |
What
Calipers To
Choose?
To
effectively
sell a product
to the customer,
application
information
is critical.
The dealer
needs to identify
the specific
make/model/year
for proper
fitment. Dealers
also need
to understand
what the customer
expectations
are. Price,
performance,
and appearance
are all equally
important.
Most
dealers are
aware of the
low cost import
products now
available.
If you’re
not sure,
always ask
the supplier
or manufacturer.
HHI brake
calipers are
designed and
manufactured
in our plant
using only
USA-made materials
and components.
|
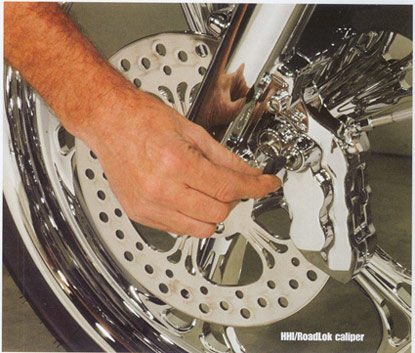 |
|
This
provides us with
complete accountability
and support for
our products. Knowing
that these products
are made in the
USA is a strong
selling point dealers
can use in making
the sale.
Caliper
differences are
mainly found in
materials and design.
Stock calipers are
generally made of
cast aluminum that
has a lower tensile
strength as compared
to billet aluminum.
HHI manufactures
all its calipers
from 6061-T6 billet
aluminum allowing
it to design a lighter,
stronger caliper.
A
recent offering
from HHI now integrates
braking with security.
The idea of attaching
a lock to the rotor
has been around
along time, but
integrating that
feature into the
caliper is a revolutionary
concept produced
by RoadLok. This
new product provides
braking and security
in one package,
which makes locking
the bike more convenient
and safer while
providing braking
improvement at the
same time.
Our
newest braking-product
line is a six-piston
caliper designed
specifically for
use with our new
13" floating
rotors. This is
also a great upgrade
over stock, especially
with the introduction
of the new braking
system using a 11.8"
rotor on the 2008
H-D touring models.
We’ve mainly
sold these as dual-to-single
disc conversions
on baggers when
installing custom
wheels.
Upgrading
to an HHI four-
or six-piston caliper
should be done on
any bike still equipped
with the 1999-and-earlier
single-piston unit.
If it came as a
stock single disc,
then a single replacement
will provide plenty
of i m p rovement
and the same goes
for the dual-disc
upgrade. Bikes from
2000 and later are
equipped with the
H-D four- piston
caliper. Customers
looking for a chrome
upgrade, and who
are satisfied with
perf o rmance, could
be sold the four-
piston version;
however, the six-piston
will give them a
performance improvement
over stock. Touring
model bikes equipped
with dual discs
will also find good
perf o rmance with
the HHI four- piston
upgrade and a significant
improvement when
switching to six-piston
calipers.
Fitments
and Upgrades
Most
distributors and
brake-pad manufacturers
have a catalog cross-
reference listing
the various fitments
for most stock and
aftermarket calipers.
If unsure, the dealer
should contact the
manufacturer for
specific fitments
as there are a wide
variety of pads
available.
Dealers
should stock the
most common bike-model
fitments, which
include left- and
right-hand front
fourpiston calipers
for both 1999-and-earlier
and 2000-andlater
versions. The HHI
‘99-earlier
caliper can also
be used for rear
applications when
assembled with HHI
rear brackets. Caliper
installations should
always be accompanied
by a brake fluid
flush service. Periodic
caliper cleaning
while installed
on the bike can
be helpful in clearing
brake dust and debris.
Most HHI calipers
feature dual seals,
one of which is
a dust seal that
helps extend the
life of the main
pressure seal.
Calipers
are best shown in
a display cabinet
or installed on
a shop bike. Promotional
literature supplied
by the m a n u f
a c t u rer and
displayed with the
calipers is an effective
way to promote the
product and educate
customers. Typical
margins for the
dealer are 25-30
percent. Brake caliper
sales can often
be coupled with
other components
such as brake rotors
and brakeline replacements.
AIR
|
|
|
|
|
|
|
|
 |
 |
|
|
|
|
|